Building out a cleanroom and adjacent environments is a multi-stage construction process and particular protocols must be maintained at each stage of the construction to insure the integrity of the cleanroom. The stages are Stage 0 — Regular Construction; Stage 1 — Clean Construction; Stage 2 — Pre Cleanroom Construction; and, finally, Stage 3 — Active Cleanroom. Following are the important steps in each stage.
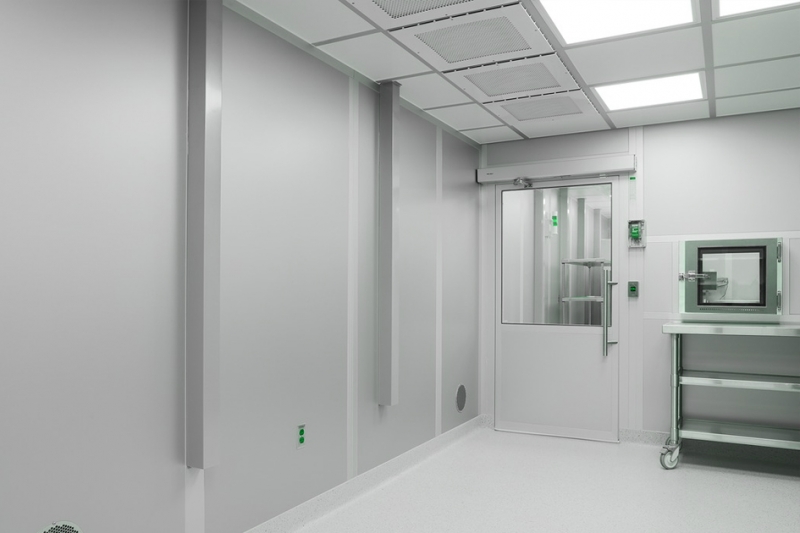
The regular construction phase is what must contractors are used to, but in the context of a cleanroom special attention should be paid to housekeeping to set the tone for cleanliness. At this stage there are no material restrictions and standard personal protective equipment, such as hard hats, safety glasses and vests, should be used. Take care to protect building materials as well. Construction workers should apply standard good housekeeping practices and complete daily and hourly clean-ups.
All drywall work should be complete if possible before the first stage of actual clean construction. During this phase, conduct daily and hourly cleanup using vacuums and start using a daily cleaning service. There should be no unnecessary trash or debris in cleanroom area and you should use multiple rugs as well as sticky mats to prevent dirt from entering. This is also when you begin to conduct particle counts.
In the second stage, control and limit access to the cleanroom area and establish a smock room/air lock for entry/exit with an air cleaner. Workers must wear booties in the area and use sticky mats on floors. There should be no wood, cardboard, or paper allowed in the area. A HEPA vac is required for all cutting/drilling in the cleanroom and the air systems should be on, but not the FFUs.
The third stage, which is for punching and finishing details, is the most restrictive. It includes all the precautions of Stage Two, plus several additional steps. At this stage, access is limited and workers must be fully smocked, including wearing lab coat or coveralls, hair/beard nets, booties, and gloves, and they must use a designated smock room. In addition to operating the MUA system, recirculation air is continuously cleaning the air.
O cumprimento de todos os requisitos específicos de uma sala limpa aumenta os custos de construção, mas isso varia consoante o tipo de sala limpa, sendo que as salas mais apertadas e restritivas são as que custam mais. Em média, a gama de preços das salas limpas varia entre $1.000 por pé quadrado para uma sala de Classe 1 e menos de $200 por pé quadrado para uma sala de Classe 100.000.
Não se deixe intimidar pelo processo de construção de salas limpas. No fim de contas, não passa de uma construção. Seguindo os planos e as especificações e respeitando as diretrizes para cada fase, a construção da sala limpa pode ser executada com êxito e com poucos problemas. Para facilitar o processo, lembre-se de que a pré-construção é extremamente importante, portanto, desenvolva um cronograma detalhado com antecedência e gerencie a aquisição com cuidado. Comunique claramente o calendário de construção a todas as partes para manter toda a gente na mesma página. Como as coisas vão mudar, esteja preparado para gerir imprevistos e seja flexível e adaptável.
Constructing cleanrooms is challenging, requiring careful attention to specific details in both design and construction procedure. Using the accepted industry standards and the UM as blueprints, however, will facilitate the successful completion of a cleanroom. Working in partnership with the cleanroom operator on the specific design assures that the resulting room will meet the needs of end users and enable them to achieve a desired ROI from the operating space.
OláPor favor, deixe uma mensagem